Leader Talk
Lean approach to better internal working regulations
Many labor-intensive manufacturers in Vietnam are looking to improve their internal working regulations (IWR) in a lean approach with a view to reducing waste while maintaining or even increasing values.
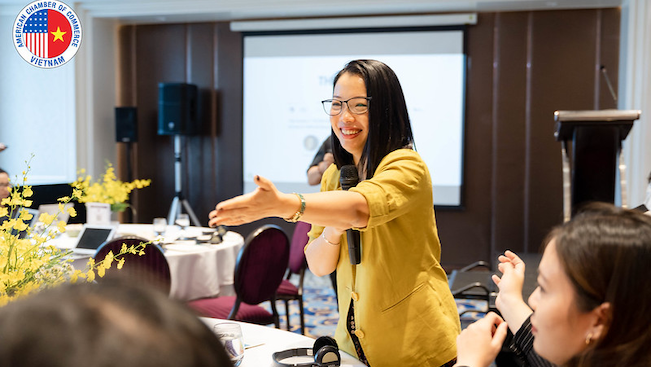
Fifty per cent of employees working at 100 companies across 13 localities in Vietnam don’t fully understand the rules and policies set by their companies, cited in Respect Vietnam’s recent survey. These companies employ over 100,000 people.
This results in miscommunication of working standards, poor workplace discipline, low labor productivity, and low business performance, including delays, disruptions, or closures during social unrest.
“It is clear that if we can simplify and prioritize the working rules and policies by adopting lean thinking, it can help enhance employee disciplines, team productivity, and business performance as the whole,” said Ha Dang, founder of Respect Vietnam, at the workshop “The Know 1: Lean thinking as part of post-Covid19 working life” organized by Respect Vietnam and AmCham Vietnam.
Yen Pham, employment labor legal and strategic employee relation manager at Intel Vietnam, said that the IWR document is often made up of dozens of pages and the content is approved by the provincial department of labor.
Developing a lean document doesn’t mean removing all the unnecessary words. Instead, it is vital to retain key messages in a coherent framework that makes it easy for employees to read, memorize ad check anytime they need, especially when they need clarity on regulations that, if violated, will be subject to fines.
The basic insight of lean thinking is to eliminate waste. Many companies wasted much time and effort on the IWR training activities. It usually takes two to four hours per employee to complete a training session. For a manufacturing company with 10,000 employees, the training time can take up a huge amount.
"If being converted into productivity, the company may lose some million products, in the meantime discipline actions are not necessarily followed. Lean thinking will help reduce training time while increasing productivity,” Yen added.
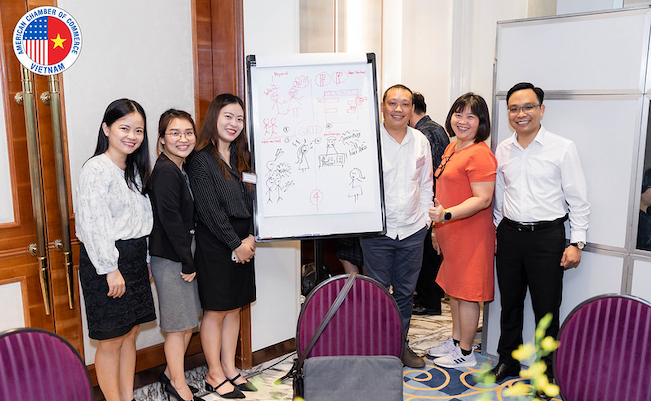
Fashion Garments is a good example of lean IWR. The company is currently managing over 10,000 employees in 8 factories. It is a challenging task to ensure the IWR training and application for all factories in a cost-effective and consistent manner. To this end, Fashion Garments has made efforts to adopt lean thinking by digitizing its workplace regulations.
Doan Hoang, head of the compliance department at Fashion Garments said that the company has decided to digitize its IWR document which is friendly to employees to optimize resources. As 95 per cent of its workers have their own smartphones, the company has designed the document for both PCs and smartphones.
"We also incorporate the latest marketing/communication trends to attract the attention of employees. During training sessions, we show a guideline video to help them navigate and access the document online. By digitalizing workplace regulations, the company has significantly reduced training time and costs while increased added value,” said Doan.
Proactive transformers earn higher returns
When organic becomes an inspiring wellbeing lifestyle
For Tyna Huynh, co-founder of Drinkizz, organic is not just a food choice but a way of life that fosters a deep connection between people, nature and community.
Garment factories embracing respectful workplaces
Embracing respectful workplaces could very well be the key to unlocking a more prosperous future for Vietnam's garment industry.
Vietnamese corporates in new era: The reborn dragon
Vietnamese businesses have had a long journey with great achievements, and this path will continue and blossom in years to come.
The future of jobs in AI era
While some jobs are expected to be replaced by emerging AI applications, the technology is broadly seen as a catalyst for positive transformation in the workforce.
Financing Southeast Asia’s energy transition
The energy transition is bringing forth new challenges, particularly in refining financial systems.
Few countries are better placed than Vietnam for consistent robust growth
Alex Hambly talks about investment opportunities in Vietnam following his appointment as chief investment officer (CIO) of VinaCapital.