National Focus
Production shift from China benefits Vietnam industrial market
Looking at the remainder of 2019 and for the full 2020, CBRE expects an increase in industrial supply across Vietnam to benefit from the production shifting from China given the former key economic fundamentals.
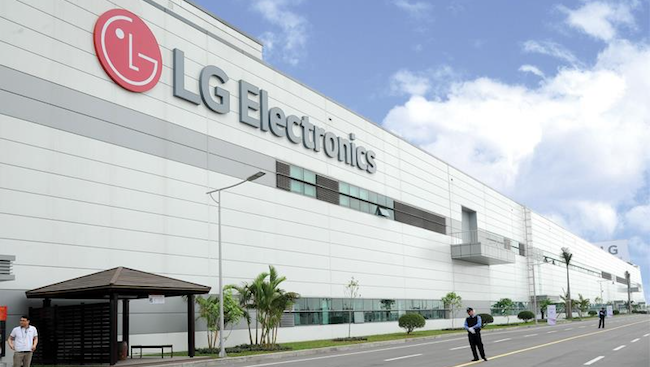
The trend of shifting production from China is not new to many as cost of production in China continues to rise which makes relocation seem like a financially viable choice to many manufacturers.
Also, according to a recent survey conducted in November 2018 by the UBS Evidence Lab, key drivers for moving export production out of China include lower environmental cost/standard, lower risk to trade war/tariffs, lower labor cost and land cost, easier access to supply chain, better infrastructure.
And relative to the size of their economies, Asean economies, especially Vietnam may be well placed to benefit from this production shifting given Vietnam key economic fundamentals including GDP growth, foreign direct investment, inflation remain positive while the country continues to invest heavily into infrastructure and help manufacturers to get better access to key export markets by participating in several bilateral and multilateral trade agreements.
These drivers are on top of Vietnam’s competitive land acquisition cost and labor cost, versus that in China and other neighboring countries, which have been underlying drivers for China+1 that several surveys pointing out.
Government's heavy investment into major infrastructure projects
According to CBRE, Vietnam government has spent billions of dollars to improve its infrastructure to help attract foreign investment. Statistics by Asian Development Bank and Bloomberg show that Vietnam’s public and private sector infrastructure investment averaged 5.7 per cent of GDP in recent years, the highest in Southeast Asia.
This direction has proven successful as improved major infrastructure projects such as new highways, expanded ports and airports, have enticed developers to follow with industrial parks being established or expanded in close distance to these infrastructures, and, in return, developers can offer this new infrastructure as part of their offering to attract occupiers from China.
There are a number of new infrastructure projects across Vietnam and its implication to the number of industrial parks in close distance. Based on CBRE findings, these industrial parks achieved good occupancy with commitment from several multinational in which infrastructure connectivity played a major role in these occupier’s location decision.
In the north, according to Jones Lang LaSalle (JLL), located only 200 km from the border to China, Haiphong is widely regarded as the China+1 manufacturing base in ASEAN to take advantage of China-ASEAN FTA.
The city has been the spotlight for FDI investment, garnering attention and support from the central authority, supported by a major infrastructure boom and numerous governmental incentives.
The Haiphong Economic Zone, which offers companies preferential treatment when they set up operations, is also acting as a catalyst to tempt more investors to the region. Hai Phong City’s infrastructure has undergone significant improvements through the completion of three core projects of Hanoi-Haiphong expressway, Tan Vu – Lach Huyen highway, and Dinh Vu – Cat Hai bridge.
Vietnam’s FTAs and US-China trade war act as a pushover
Vietnam has signed many agreements, including bilateral and multilateral agreements, with many nations. These trade agreements allow removal of duties among member countries which help attract more manufacturers to set up production in Vietnam to retrieve tax benefit when they export to those markets.
The US tariffs upon China coming on the on-going trade war between these two countries is equivalent to a scenario of Vietnam essentially possessing a free trade agreement with the US and Vietnam also poses a lower risk to trade war than China.
There is a fact that all Chinese products would be subject to an additional 25 per cent tariff when Chinese products are hindered from export via that level of tax. This is equivalent to a scenario of Vietnam essentially possessing a free trade agreement with the US.
It also means, in the short term, that Vietnam key exports like textile and garment, footwear, mobile phone, consumer electronics, wooden furniture, fisheries, bags, suitcases, and machinery could find better access into the US.
TVs, mobile phones and several wearable technology items are not yet included in the current tariff list and occupiers in these sectors, especially big occupiers would look to relocate part of their supply chain to Vietnam to mitigate the trade war risk as well as to tap on the country remained competitive cost.
For instance, the number of factories in Vietnam listed in Apple supplier list increased from 16 in 2015 to 22 in 2018. All of them are FDI companies.
Samsung Electronics Co Ltd, the world’s biggest smartphone maker, said late last year it would cease operations at one of its mobile phone plants in China, according to Reuters. Currently, 29 Vietnamese companies act as Samsung’s Tier-1 supplier.
LG Electronics Inc said it would stop producing smartphones in South Korea and move manufacture to Hai Phong, Vietnam. The move will boost annual production capacity of its smartphone plant in Vietnam by 83 percent to 11 million handsets from the second half of 2019.
Looking at the remainder of 2019 and for the full 2020, CBRE sees an increase in industrial supply across Vietnam to benefit from this production shifting from China.
To well position themselves to cater to increasing demand, foreign developers would look for local partners with experience and big land bank to help fast track their market penetration.
As an example, a joint venture between Becamex and Warburg Pincus to form BW Industrial that can offer ready built & built to suit factories and warehouses in strategic locations in Vietnam.
Also, as market and occupiers are getting more sophisticated, developers would need to provide a variety of products, land lease, ready built factory & warehouse, built to suit facilities and sale & lease back to bring more value to their clients.
For ready-built factory in certain strategic locations, CBRE also sees that products specification can evolve from traditional and conventional single story to multiple floors factories, ranging from 2 to 6 floors.
While high rise stock in the market is still limited, this could be a new trend as Vietnam desires to attract higher technology and light industries which demand high spec quality industrial spaces.
Thai tycoon unveils strategy for largest industrial park in Vietnam
Resolution 68: A turning point in Vietnam's private sector policy
As Vietnam sets its sights on becoming a high-income country by 2045, Resolution 68 lays a crucial foundation. But turning vision into reality requires not only good policy - but also unwavering execution, mutual trust and national unity.
Vietnam plans upgrade of Gia Binh airport to dual-use international hub
Vietnam plans to upgrade Gia Binh Airport in Bac Ninh province into a dual-use international airport to support both military and civilian operations, the government said on Friday.
Lives under the scorching sun: Outdoor workers racing against climate change
Under unforgiving conditions, the outdoor workers - the backbone of urban economies - endure the harshest impacts of climate change while remaining overlooked by social safety nets. Their resilience and struggles highlight the urgent need for better protection in the face of rising temperatures and precarious livelihoods.
CEO Group chairman unveils guide to Vietnam real estate for foreigners
Doan Van Binh, Chairman of CEO Group and Vice President of the Vietnam National Real Estate Association, introduced his latest book, “Vietnam Real Estate for Foreigners,” at a launch event in Hanoi on Friday.
Women leading the charge in Vietnam's green transition
Acting for increased women’s participation and leadership in climate action, Vietnam can accelerate a transition that is more inclusive, just, and impactful.
Steam for girls: A journey of passionate and creative girls
The "Steam for girls 2024" competition provides a creative platform for Steam and an opportunity for students to connect with peers from various regions within Vietnam and internationally.